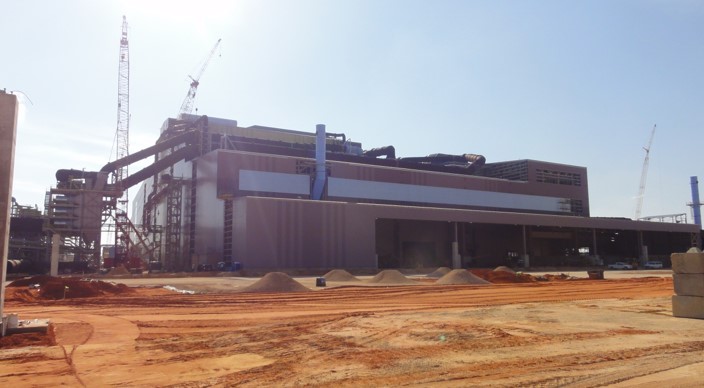
Market
Steel
Client
Outokumpu Stainless USA, LLC
Location
Calvert, AL
State-of-the-Art Melt Shop
RTP played a pivotal role in the successful installation of a cutting-edge "Greenfield" stainless steel melt shop in Calvert, Alabama, boosting the production capacity to an impressive 900,000 tons of high-quality steel slabs. This transformative project significantly enhanced Outokumpu Stainless USA's competitive edge in the market. As a trusted partner, RTP brought together a multidisciplinary team, delivering comprehensive engineering and project management services. Employing advanced technology, we crafted a precise 3D model, ensuring seamless execution and fostering a seamless collaboration between all stakeholders. Our commitment to excellence drives our mission to provide the utmost value to our esteemed client.