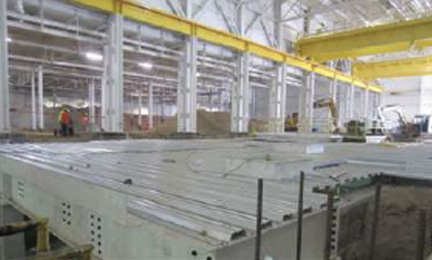
Market
Automotive
Client
Aristeo Construction Company for General Motors Powertrain
Location
Bedford, IN
Upgrade and Refurbishment of General Motors Die Cast Buildings
RTP played a vital role in the successful upgrade and refurbishment of several 42-year-old General Motors Die Cast Buildings. The project involved replacing foundations for 2500-ton Die Cast Machines with ones designed for 4000-ton machines, which were positioned over a 30-foot-wide tunnel. Additionally, all process equipment was removed, and the concrete floor, support steel, piping, HVAC, and electrical systems were replaced.
RTP's actions encompassed a wide range of tasks and responsibilities to ensure a seamless and successful project execution. We assisted in developing the Plant Layout for the new equipment in the Die Cast South facility, optimizing space utilization and workflow efficiency. RTP's engineering team developed structural design drawings for various components, including foundations and inertia blocks for the 4000-ton capacity Die Cast Machine and the 200-ton capacity Rollover Trim Press. The design also included support beams spanning the 30-foot tunnel to accommodate the significant loads with limited deflection. Furthermore, RTP designed the tunnel roof/process floor, oscillating scrap conveyor foundations, incline scrap conveyor foundations, high load path and floor area for the die cart, and specified conduit and pipe embed sizes and locations for the die cast machines and automated cells. To aid in visualization and coordination, RTP provided 3D models of the work to the client for incorporation into the master plant 3D model.
Throughout the construction phase, RTP provided on-site assistance, particularly in addressing unknown abandoned foundations that were discovered during the process. Our team also prepared specifications for equipment purchase, facility refurbishment, and equipment installation, ensuring clear guidelines for the project. RTP conducted design reviews, offering comments on the building refurbishment to ensure quality and compliance with project objectives. We also reviewed building crane requirements, evaluating reach and tool path for changing 50-ton dies, and assessed the need for crane replacement. RTP ensured the proper placement of equipment near crane reach and travel path to avoid interference and optimize operations.
The project resulted in improved foundation structures, enhanced equipment capabilities, and modernized facility infrastructure.