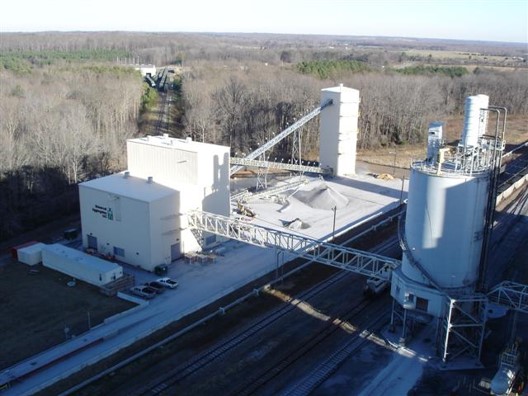
Market
Material Handling, Light Industrial
Client
Universal Aggregates LLC
Location
King George, VA
Birchwood Manufactured Aggregate Plant
RTP was engaged by our client to develop a manufacturing plant that would convert coal combustion by-products from power plant scrubbers, into lightweight aggregate for masonry blocks or concrete. The facility consisted of a process plant area housing the ash storage pneumatic transfer, additive bins, pug mill with sealer and extruder, impactor, screens and all necessary material handling equipment. Our team provided comprehensive installation engineering services including all drawings, specifications, procurement, permitting, project management, and construction management.